Numerical simulations (external aerodynamics, civil engineering, hydrodynamics) using OpenFOAM are currently under investigation at CFS Engineering.
Stephane Sanchi participated in a 3-days course 'CFD with OpenFOAM' in Lucerne (11-13/02/2009).
OpenFOAM is an open source computational fluid dynamics (CFD) toolbox. Its main features are utilities (pre- and post-processing, tools for mesh converter and mesh generation, ...), solvers (incompressible flows, compressible flows, multiphase flow, heat transfer, solid dynamics, ...) and libraries (turbulence models, chemical kinetics, ...).
ANSYS ICEMCFD HEXA software is used to generate fully hexahedral structured meshes. Another option is to use the OpenFAOM mesh generation utility called snappyHexMesh.
For post-processing the ParaView application is used. ParaView is an open-source, multi-platform data analysis and visualization application. ParaView users can quickly build visualizations to analyze their data using qualitative and quantitative techniques. The data exploration can be done interactively in 3D or programmatically using ParaView's batch processing capabilities.
Numerical simulations using OpenFOAM for various kinds of ma rine applications (ailing vessels, planing hulls, ships and marine propellers) are under investigation at CFS Engineering.
The following are some examples of computations done with OpenFOAM :
1. Air Flow Around the Superstructure of a Motor Yacht
We have modelled the air flow around the superstructure of an 15m motor yacht. Flow behaviour over the aft decks of the motor yacht was of primary interest. The process leading to better understanding of the flow is composed of successive steps: CAD import and cleaning, grid generation, CFD computations and post-processing of available data. Various wind configurations similar to offshore conditions were selected. Using dedicated post-processing tools we can point to specific areas on the superstructure where modifications may be applied in order to redirect the flow. In particular, streamlines and peak pressure spots help us determine where modifications can be applied to change the flow behaviour over the geometry and increase the comfort of the passengers onboard.
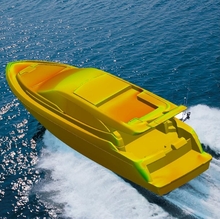
The image above shows pressure contours around the motor yacht at cruising speed. More information about these computations are available here.
2. Air Flow Around a Planing Craft
Air flow a round a planing craft has been modelled using the same methodology as presented and explained above. Computations have been performed with a fixed trim. Usefull results like drag resistance, lift and moments help naval architects improve and optimize their design shapes.
The images above and below show pressure contours around the exposed part of the planing craft at a targeted speed of 48 knots.
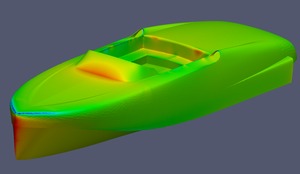
|
More detailed information about this can be found at following links:
Corsier-Port Boatyard and
sebschmidt architecte naval sarl.
3. Flow Around a Cut Sphere with Free Surface Elevation This example shows the capabilities of OpenFOAM for multi-phase flows (air and water). The mesh was generated using ICEM hexa with particular care given at the interface between the two fluids.
Details of the surface mesh: front and back views of the cut sphere
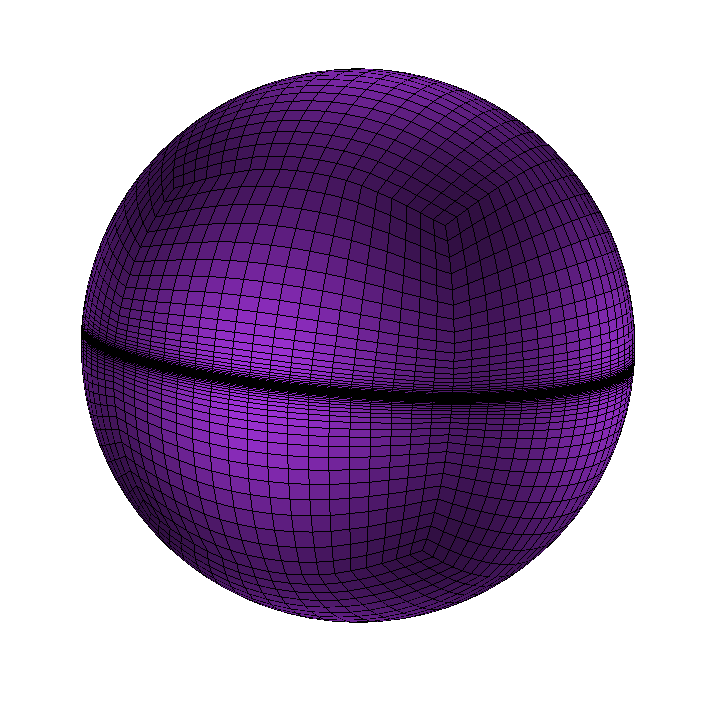
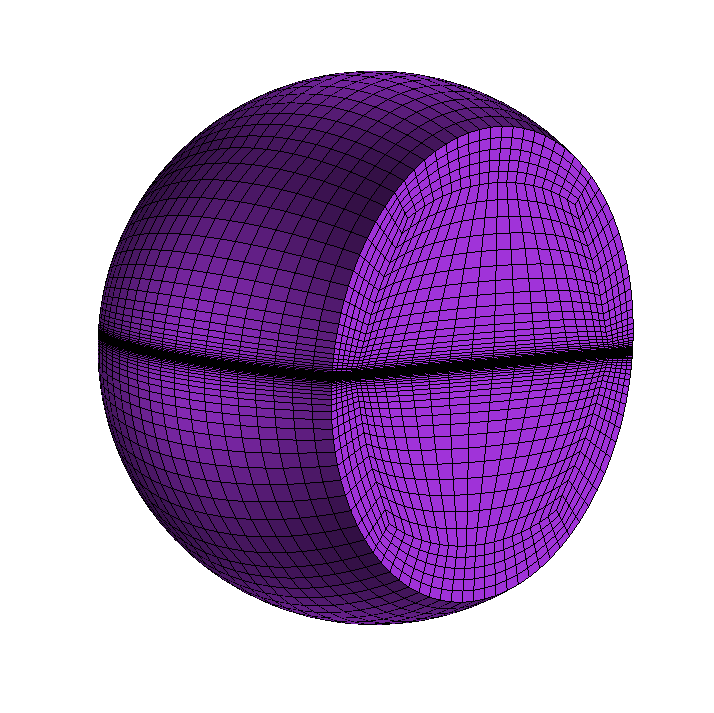
Plane cutting the sphere:
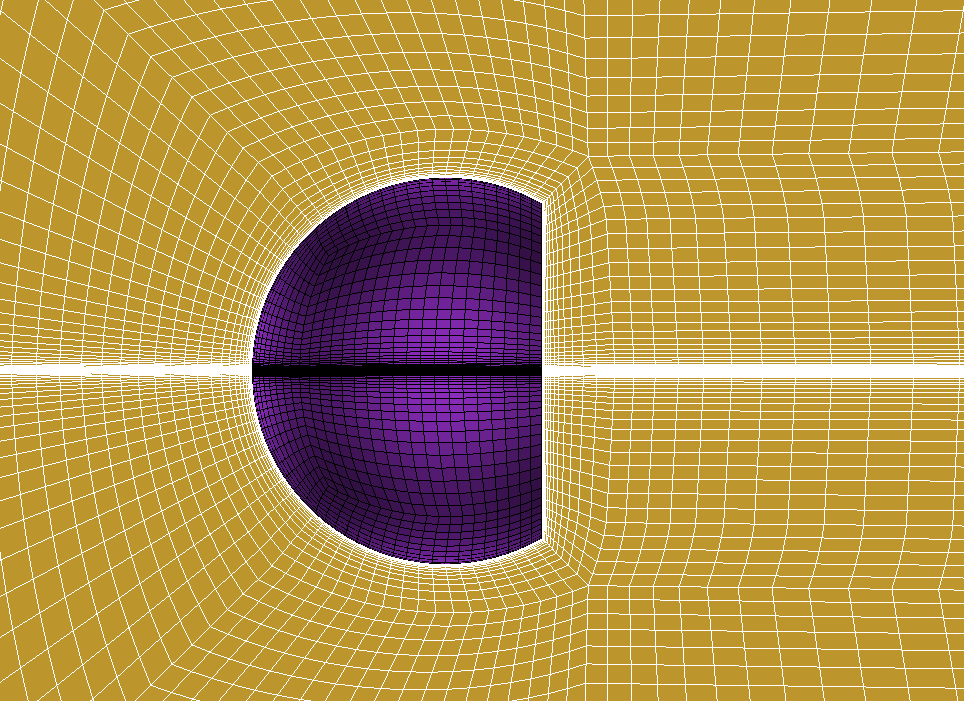
The OpenFOAM computation has been carried out using the interFoam solver in parallel mode with standard settings (inlet velocity 5 m/s, kOmegaSST turbulence model, adjustable time step feature, maximum Courant Number 0.8 and computation time 20 sec). The following videos show the free surface elevation on the symmetry plane (opacity 0.7) and on the cut sphere.
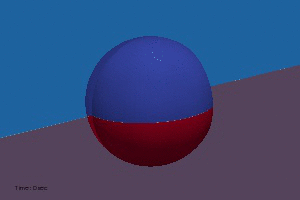
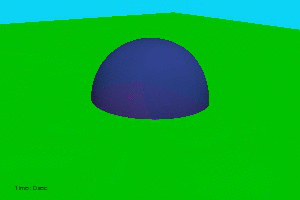
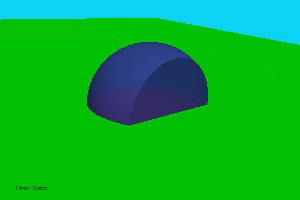
The above animations present the free surface wave pattern around the cut sphere (opacity 0.7). Movies have been generated using the ParaView software. This computation done with a simple geometry (cut sphere) shows that this solver is able to compute flows around boat-type geometries and thus estimate force components (in particular drag).
4. Implementation of an Actuator Disk in OpenFOAMAn actuator disk simulates the effect of a rotor. It is needed when we want to know how it affects its surroundings. An Actuator disk region is defined where the rotor is accounted for by adding momentum (volume force) to the fluid.
The fan boundary condition is implemented in OpenFOAM. This method requires a fan patch in the mesh and has some limitations. Thrust can be modeled, but torque can't be (no swirl). Uniform thrust is added as a function of velocity through the fan. To summarize, the fan boundary condition adds only a pressure jump in the flow direction.
An actuator disk model was implemented by
Erik Svenning (Chalmers University of Technology). With minor modifications it runs using OpenFOAM-2.0.x version. Main requirements for such a model are: possibility to add non-uniform thrust, possibility to add non-uniform swirl and possibility to define an actuator disk region without modifying the mesh. This method assumes that thrust and torque are known. Volume forces, in the axial and tangential directions, are computed assuming that the force distribution follows the Goldstein optimum distribution. Following pictures show contours on a plane cutting the flow domain of a basic test-case. The gray object represents the outer surface of the actuator disk.
Pressure:

Velocity magnitude:

Streamlines collored by angular velocity:


Twisted streamlines indicate that swirl is being imposed on the flow field.
5. Hydrodynamic Analysis of Marine Propeller The aim of this study is to evaluate the possibility to use
OpenFOAM for computing the flow around rotating devices, and in particular around immersed marine propellers. Forces induced by the propeller, solver stability and computational time were among principal interests.
Using OpenFOAM, we have modeled the flow around a 5-bladed marine propeller. We were interested in the hydrodynamic flow behavior around shaft, hub and propeller blades.
Some effort was put to clean properly the CAD geometry to obtain water-tight surfaces. Computational domain boundaries were fixed far enough to avoid any flow perturbations.
The multi-block structured grid was generated using the ICEM Hexa software. The following pictures show the surface mesh and a scan plane cutting the propeller amide its width.
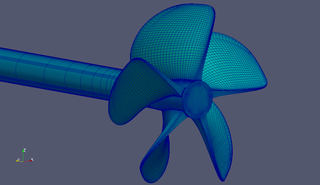

2 different solvers were used to compute the flow around the marine propeller: MRFSimpleFoam (steady-state solver) and pimpleDyMFoam (transient solver). Both standard solvers are available in the OpenFOAM-2.1.x distribution. A new arbitrary mesh interface (AMI) has been recently implemented. Hence it allows simulations with sliding interfaces and enables rotation of geometry parts.
The following videos show results obtained with the transient solver pimpleDyMFoam. 5 revolutions have been simulated.
Pressure field:
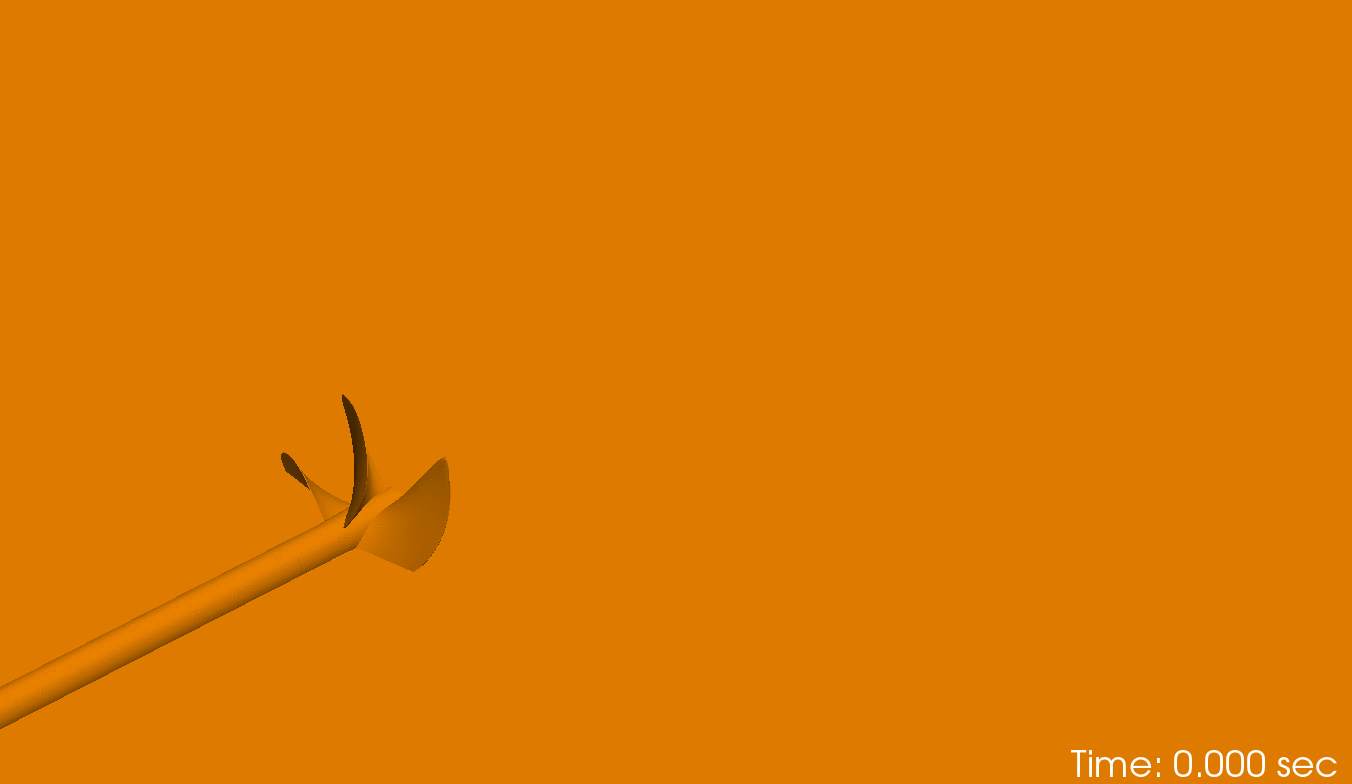
Streamwise velocity field:
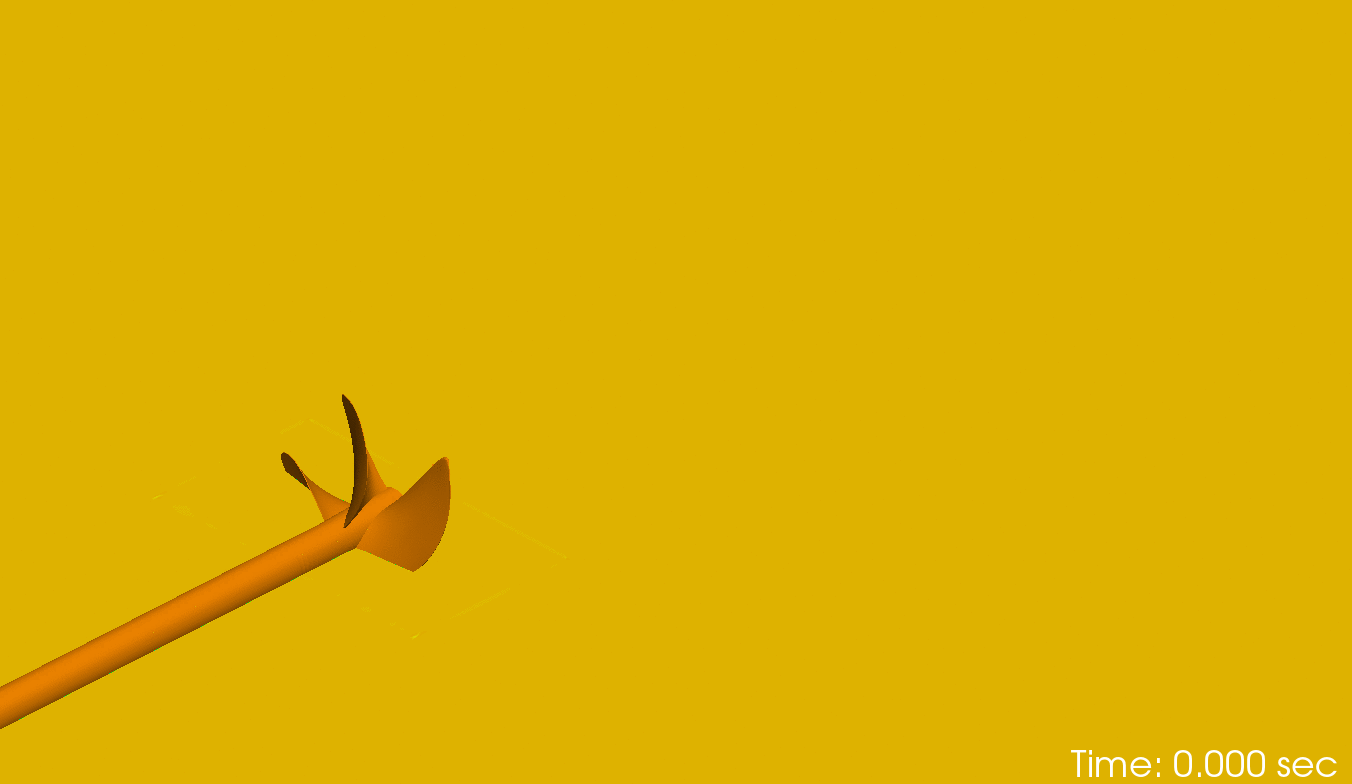
Streamwise velocity field on 3 vertical planes:
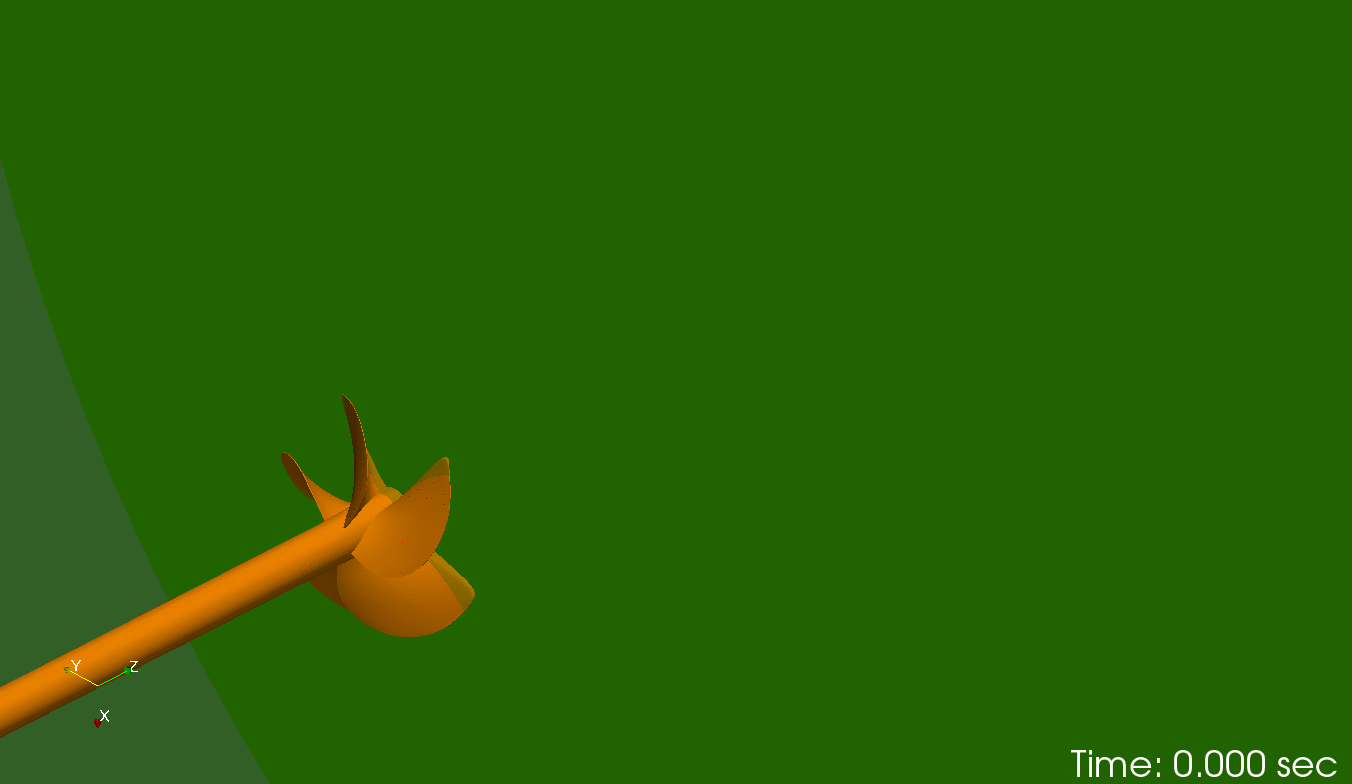
More information can be obtained by writing an email to
Stephane Sanchi.
6. Aerodynamic Study of the Ahmed Body (with 12.5 deg. slant angle)The mesh was generated using the snappyHexMesh (sHM) utility. sHM generates 3-dimensional meshes containing hexahedra and split-hexahedra automatically from triangulated surface geometries in STL format. The mesh approximately conforms to the surface by iteratively refining a starting mesh and morphing the resulting split-hex mesh to the surface. There is an optional stage of the meshing process which introduces additional layers of hexahedral cells. The snapEdge utility, a tool developed by
Niklas Nordin, was inserted used and into the mesh generation process. It modifies the mesh to obtain sharp edges where necessary. The following pictures show the mesh generation step by step. Left pictures are front views and right pictures are rear views.
First step : cell splitting at feature edges and surfaces (sHM)
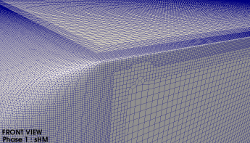
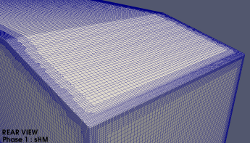
Second step : snapping to features on STL surfaces (snapEdge)
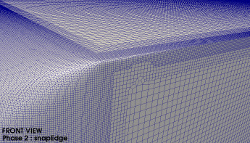

Third step : add layers (sHM)
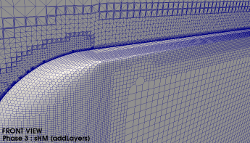
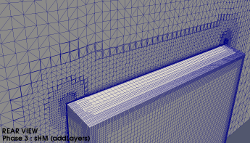
These OpenFOAM computations are currently underway at CFS Engineering.
7. Example of Particle-Tracking Discrete Element Modeling (DEM) are numerical methods for computing the motion of a large number of particles of micrometre-scale size and above.
In
OpenFOAM an implementation of the discrete element method has been introduced for particle simulations.
The implementation of discrete element method includes the following features: detailed collision models that can include deformation, friction, rolling, cohesion, etc., each particle can undergo multiple, simultaneous collisions (collision between particles, collision of particles with walls), particles retain information about current collisions from one time step to the next, different sized particles, runs efficiently in parallel with no restriction on the shape or size of mesh cells, and with interactions occurring between particles (and walls) in non-neighboring processor domains.
The icoUncoupledKinematicParcelFoam solver (transient solver for the passive transport of a single kinematic particle could) has been used to compute the emptying of an hopper. This example is one of the many tutorials provided with the OpenFOAM package. The hopper geometry is bi-dimensional. The computational grid has been generated with the blockMesh utility. Then the cloud (of particles) positions have been defined and set as initial state condition.
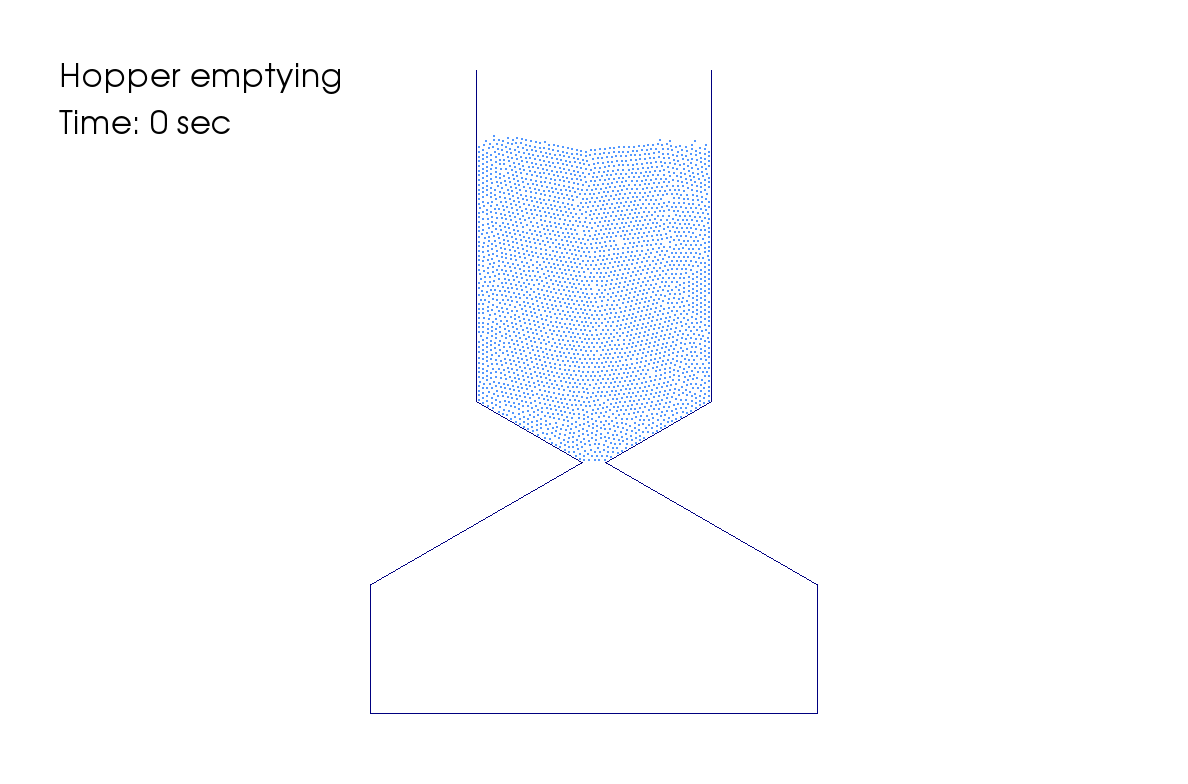
Only particle-particle interaction is considered. Any coupling between fluid and particulate phase is neglected. The above animation, done with
ParaView, shows the emptying of the hopper.
Last update: 18.03.2013